Vehicle and frame structures
Rather than focusing on the strength assessment of a detail, we aim to ensure standard- and specification-compliant verification and optimisation of the overall system structure.
IBAF supports rail vehicle and frame structure development processes through application of its many years of in-process and final design validation experience. As a basic prerequisite, we offer full familiarity with, and detailed knowledge of, all relevant standards, codes of practice and regulations.
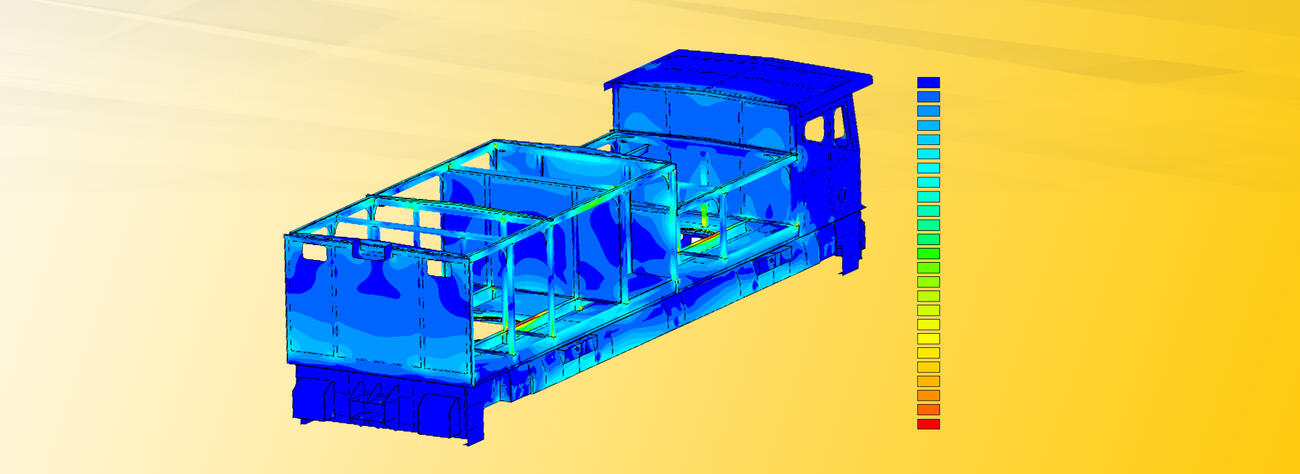
Range of services
We support manufacturers and operators in the following fields:
- Simulation of rail-bound vehicles
- In-process computational engineering for strength assessment and structural optimisation
- Final strength and damage verification according to industry-specific regulations
- Evaluation of the vibroacoustic behaviour of structures
Our choice of simulation tools (manual/analytical, MSA, FEM, MBS, FEMFAT®) is always properly aligned to the problem in hand. From simple manual calculation for nominal stress assessments to high-level non-linear FE models, we are equipped for every eventuality.
Integrated system simulation with component load analysis
Not every component of a vehicle structure experiences the same stresses. At the local level, different system configurations and stress patterns can be critical. In view of this, whole-system simulations are used to derive design relevant component loads, allowing each component to be proven individually and with fewer load cases. Depending on the structure and operating conditions, the following procedures are applied:
- Matrix structural analysis (MSA) modelling with definition of all the positions and load case combinations
- Model-based simulation (MBA) with definition of the masses and flexibilities relevant to dynamic behaviour
- Coupled simulations incorporating the drive and control technology
Fatigue strength analyses, stability verification and strength optimisation in respect of locomotive frames, carriage bodies and bogies
Development-related calculations and analyses
Structure optimisation can be more readily attained where the development work is accompanied at an early stage by the appropriate computations and analyses. Efficient models need to be developed, calculated, effectively evaluated and structurally optimised within a short time through iteration steps. Our approach involves the following:
- FE model structures with simple local adaptability to structural design upgrades
- Efficient substitution modelling for complex connecting and interface elements such as bolted joints, antifriction bearings, elastomer mounts – with accurately tailored degrees of simplification
- Algorithmic evaluation tools with full validation for fast strength assessment of the integrated assembly in accordance with accepted standards and codes of practice
Final verification
Whether for documentation purposes, approval or certification, the final as-manufactured status also needs to be fully validated. For this, we offer a range of services, including:
- Completely documented strength verification analyses in accordance with the FKM guideline for analytical strength assessment of mechanical components
- Verification according to railway-specific standards and regulations such as DVS 1612, DIN EN 12663, DIN EN 13979, DIN EN 13749
- FEMFAT® damage analyses using load time series
- Validation in accordance with e.g. German DBE and BGE regulations
Acoustic optimisation of rail vehicles
On the basis of measurements performed on existing systems, an acoustic understanding of the structural complex can be developed for the purpose of deriving specific problem-solving and optimisation approaches. The data thus acquired enable identification of relevant excitation sources, transmission paths and emission locations in the structures.
- Sound pressure measurements with acoustic camera
- Combined sound pressure and intensity measurements
- Structure-borne and transfer path analyses
- Experimental modal analysis
In addition, vibroacoustic simulations will invariably be implemented at an early phase of the process to specifically facilitate the development of quiet vehicles. We support the client’s concept and layout definition work as well as the selection and design of e.g. hoods, screens, silencers and insulation systems through the following:
- Modal analyses (MSA, FEM, MBS)
- Frequency response analyses (FEM, MBS)
- Calculation of the radiated sound field (BEM)
- Noise predictions
And IBAF can also offer the engineering, design, manufacture and supply of tailored solutions for noise reduction.